Glass research
- Nathan Kerswill
- Apr 24, 2017
- 6 min read
Frit casting
Frit casting is one of the simplest glass casting methods. It does not require special casting moulds. Any

fusing mould will work for this process. Prepare the mould with a separator or kiln wash before beginning the procedure. Frit compacts as it becomes molten in the kiln. As the frit is heated up inside a kiln, all the tiny air spaces are filled with the melted glass. Since it settles down into the mould, the process may take several firings depending on the outcome you wish to achieve.
frit casting, glass casting, casting moulds, frit
Keep in mind that the larger the frit used the more it will melt down into the mould. So it makes sense to use smaller pieces of frit for less compacting.
Firing the casting is basically the same as normal glass fusing. It is customary to heat up the glass at about 300 degrees per hour and hold the piece at about 1200 degrees Fahrenheit for about 30 minutes. After that the piece can be taken up as fast as possible until the full temperature is reached. Once you have reached a full fuse, soak the piece for a period of time depending on the size of the piece that is being fired.
There are a few ways to accomplish obtaining a full mould of glass when doing frit casting.
1. The easiest way to obtain a full mould is to allow the first firing to transpire and then refill the mould and heat the glass up again. This may take several firings until the mould is completely full.
2. Another way to accomplish a full mould is to build up the frit so that when it settles down it fills the mould. This method may require that you build up an access of frit onto the mould before firing.
3. The final way to obtain a full mould would be to add more glass while the kiln is still hot. When the frit has settled down inside the mould more frit can be added to the piece. This approach requires that you reach inside a torrid kiln, so high temperature gloves, IR/IV eye-wear is necessary, and of course safety precautions. Turn off the kiln before adding more glass to avoid getting shocked. Since frit is tiny pieces of glass, there is no problem with thermal shock.
Hot Casting
Hot casting is not for the novice. Although it is another form of casting glass, it requires not only a furnace

to heat the glass, but other instruments that are not used in regular glass fusing. There are also safety precautions when working with glass that has been heated to this high temperature.
Glass is heated to a temperature higher that can be achieved in a kiln or even by blowing glass. The temperature is usually around 2350 degrees Fahrenheit. Once heated the glass is scooped out of the furnace with special large ladles and poured into a mould designed for this technique.
To withstand these sudden hot temperatures, the moulds are made of ceramic and silica or resin, silica sand and a catalyst. These materials can withstand these high temperatures. The materials are mixed together and then hardened. Once mixed, they possess a sandstone consistency.
This material can be carved with various tools to design and achieve the desired depth or texture. This requires a free hand or sculptural talent to manoeuvre the material. There is no problem with undercuts and even the elaborate details are achievable with this method, because the molten glass is poured into the mould. As the glass is poured into the mould, it fills all the tiny areas even the fine details are obtained.
The moulds are not reusable however, because they are destroyed in the final process. Of course, this makes each piece one-of-a-kind and irreplaceable. Because the glass is thick, it passes over 95% of the light that strikes it and it is a solid structural component that is almost unbreakable.
Lost wax casting
In the lost wax method, each piece starts out as a wax sculpture. This is called the positive form. The
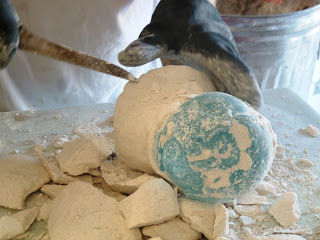
sculpture or positive form is then cast into a refractory aggregate. This refractory aggregate is made using gypsum plaster, which is plaster of Paris or silica flour. They call this process investing.
The wax is then melted or steamed out of the mould, which then forms a cavity of the original form. This cavity is now filled with glass and fused. Once the glass has cooled the plaster is scraped away revealing the glass form.
The first step is to make the wax model. There are many different ways to make the positive was form. It can be modelled or carved out of just about any type of mouldable wax, even beeswax. Since the wax is so easy to work with even household items can be used to add details and depth to the piece.
Once the wax model has been made it is encased with plaster or some other refractory aggregate to make the mould. The wax is then melted out leaving the new form out of plaster. Once the wax has been released, the mould needs to be processed and fired to cure the piece. It is now ready to receive and mould the glass.
Fill the piece with frit or the desired glass and fire the piece. As the hot glass gets molten inside the kiln, it will then take on the shape and design of the mould. Anneal and cool depending on the size and shape of the finished product.
Pate de Verre
Pate de Verre became popular about a century ago, but actually began with the ancient Egyptians. When

translated, it means “glass paste”. This process involves making a paste out of glass and a liquid binder or adhesive. Once the right texture is achieved, the mixture is placed inside a mould and then fired inside a kiln. It is a form of casting glass.
Because the glass is mixed with a liquid or adhesive it remains where placed inside the mould. This allows for the precise placement of various colours inside the mould. Normally the glass would shift during the firing process, but the adhesive keeps it in place.
Traditionally glass powder or small frit is used to make the paste. Large pieces of glass or frit would not mix and hold as well as smaller pieces.
A mould is coated with several layers of kiln wash or release and allowed to dry. Then the paste is prepared for the process. If using powder for your paste be sure to wear a dust mask or use a respirator to prevent inhaling the tiny minute particles.
Special glues can be purchased to mix with the powder or frit. Some alternatives would be watered down white glue, Aloe Vera or gelatine that has been diluted with distilled water.
Apply the freshly mixed glass paste to the mould with either a palette knife or brush. The initial coating can be fired to a tack fuse or just allowed to air dry. Use a hair dryer to dry the paste faster. Once the first layer has dried a second layer can be added. The thickness of the two layers should be about 1/8 inch in depth. Be sure to pack the second layer down lightly. Repeat process until desired areas are filled.
Sand casting
Sand casting is an old technique. It involves creating a mould and then pouring molten glass into the

vessel. The casting mould is made of silica sand that is mixed with a binder or clean sand and a small amount of bentonite. It is a compacted mould that once used it is not usable again.
This method requires access to a furnace as well as a kiln and lots of safety precautions. Wear protective clothing such as high temperature gloves and cotton clothing. It is important that your eye wear is sufficient for the high temperatures of the furnaces.
The mould is generally supported by a template made of wood or some other object. The impression made in the sand forms the mould. Molten glass is scooped from a furnace and then ladled into the mould. The glass is well over 2100 degrees Fahrenheit. This high temperature allows the glass to flow freely into the mould.
During this process, other compatible objects can be placed into or on the glass to give the appearance of a floating object inside or on top of the glass.
Sand can also be used to add a design or texture to glass, although this is not actually casting. Place the mixture into the kiln and place the glass on top. Designs can be imprinted into the sand but keep in mind that any raised areas will become depressed by the weight of the glass, while any dented areas will allow the glass to slump into the shape. This is not actually casting, but using the sand as a designing and texturing material.
References
https://amyorangejuice.wordpress.com/tag/frit/
http://roisindebuitlear.com/roisin-de-buitlear/tag/antique-glass/
http://washingtonglassschool.com/category/lost-wax-casting
http://www.bullseyeglass.com/coldwork/basic-pate-de-verre-bowl-los-angeles-1643.html
http://www.saltglassstudios.co.uk/sand-glass-casting/
http://www.glass-fusing-made-easy.com/frit-casting.html
http://www.glass-fusing-made-easy.com/hot-casting.html
http://www.glass-fusing-made-easy.com/lost-wax-method.html
http://www.glass-fusing-made-easy.com/pate-de-verre.html
http://www.glass-fusing-made-easy.com/sand-casting.html
http://www.glass-fusing-made-easy.com/casting-glass.html
Comments